When designing ships using a CAD system, profile endcuts play a crucial role in ensuring proper assembly, welding, and structural integrity. Endcuts define the specific shape applied to the ends of structural profiles, allowing for precise connections and optimized manufacturing processes. This post explores the fundamentals of endcuts, their classification, and how they are managed in ship design software. It is particularly useful for ship designers and CAD software developers aiming to enhance efficiency and accuracy in shipbuilding.
What is an Endcut?
An endcut refers to the processed shape at the end of a structural profile, such as a flat bar or stiffener, after cutting from a raw material. These cuts are essential to achieve the intended fit-up, avoid excessive gaps, and ensure efficient welding and assembly in ship construction. Properly applied endcuts contribute to reduced rework, better material utilization, and improved structural performance.
How Endcuts are Defined in Marine CAD Systems
Ship design software includes predefined endcut standards that allow designers to select or customize endcuts based on project requirements. The endcut shape is controlled by three key elements:
1. Endcut Type
Each endcut follows a specific geometrical pattern and is assigned a unique type number within a predefined range.
2. Standardized Parameters
Certain parameters, such as radii or angles, have predefined values based on endcut codes. These values ensure consistency and compatibility with shipyard standards. These parameters are typically stored in a database and cannot be directly modified by designers.
3. Explicit Parameters
Additional parameters, such as cut lengths and angles, can be manually specified by the designer or automatically calculated based on the profileโs connection details. This allows for flexible customization when standard options do not meet specific project requirements.
Endcut Codes and Customization
Endcut codes define specific instances of an endcut type with preset parameter values. Designers can choose from a library of predefined endcut codes or modify parameters to suit particular needs. For example, an endcut code might specify:
- R1 and R2 (radius values): Control the rounded edges of the cut.
- Angle values: Determine the slant or bevel for optimal welding.
- Length dimensions: Adjust endcut sizes for specific structural connections.
If explicit parameters are not provided, the system can calculate them automatically based on the connection type. This automation reduces manual input errors and ensures consistency across the design.
Example: Flat Bar – Endcut Code 1112
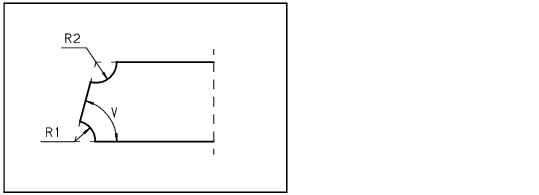
- R1 = 35, R2 = 35 (predefined radii values)
- V (angle) = Automatically calculated or manually set by the designer
Why Endcuts Matter in Shipbuilding
Endcuts significantly impact the efficiency of ship construction by ensuring:
๐น Welding Quality
Well-defined endcuts optimize welding penetration and reduce distortion, improving overall weld strength.
๐น Assembly Precision
Standardized endcuts improve alignment during assembly, reducing fitting time and minimizing errors.
๐น Structural Integrity
Properly applied endcuts minimize stress concentrations and enhance the long-term durability of ship structures.
๐น Manufacturing Efficiency
Predefined endcut standards facilitate automation, reducing manual intervention and optimizing material use.
๐น Seamless CAD Integration
Ship design software allows easy selection and automation of endcuts, improving workflow efficiency and reducing human error.
Considerations When Applying Endcuts
While endcuts offer many advantages, their implementation requires careful attention to:
โ Software Capabilities
Not all CAD systems allow for full endcut customization, which may require additional programming or workarounds.
โ Fabrication Constraints
Certain endcuts may be difficult to manufacture, depending on the available cutting technology and material limitations.
โ Standardization Across Projects
Different shipyards may have their own endcut standards, necessitating alignment to ensure consistency in design and production.
Conclusion
Endcuts are a fundamental aspect of ship design, directly impacting fabrication efficiency and structural performance. Modern CAD systems provide powerful tools for defining, managing, and automating endcuts, improving accuracy and reducing production time. By understanding and applying endcuts correctly, ship designers and software developers can enhance both design precision and shipbuilding efficiency.