π’ In shipbuilding, structural members often need to penetrate other plating elements to ensure continuity and structural integrity. These penetrations, known as cutouts, are essential for assembling stiffeners, longitudinal frames, and other structural components. Additionally, clips (also called collars) are often required to reinforce and seal these cutouts. This post provides an in-depth look at cutouts and clips, their classification, and how they are managed in marine CAD systems.
Cutouts in Marine CAD Systems π©
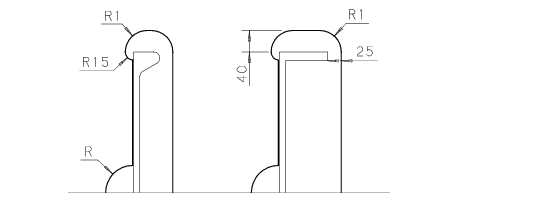
Definition and Function
A cutout is an opening in a plate or structural member that allows another profile to pass through. Common applications include:
- π Longitudinal frames passing through bulkheads or decks
- π Stiffeners intersecting with other structural elements
- β Double-bottom floors accommodating structural penetrations
Cutouts ensure that profiles fit correctly while maintaining clearance for welding and assembly. They also help distribute stress efficiently, reducing weak points in the ship structure. Properly designed cutouts prevent stress concentration, minimize fatigue failures, and improve ease of assembly during ship construction.
Standardization of Cutouts
Cutouts are typically standardized based on:
- π Geometric shape (rectangular, circular, elliptical, etc.)
- π© Radii and clearances (ensuring smooth fitting and proper weld gaps)
- π Profile type dependencies (cutouts are adapted based on the dimensions and geometry of penetrating profiles)
- π Manufacturing considerations (cutout edges may be beveled or rounded to enhance welding quality and reduce stress concentration)
Because of their repetitive nature, cutouts can be automatically generated in marine CAD systems using predefined rules and parameterized macros.
Cutout Generation Methods
Marine CAD systems provide three primary methods for generating cutouts:
1. Predefined Standard Cutouts π
Many shipbuilding CAD systems include a library of predefined cutouts that follow industry standards. These cutouts are hardcoded into the software and can be selected based on project requirements.
2. Customizable Standard Cutouts βοΈ
Most shipyards use a set of common cutout designs but modify details like clearance, radius, or shape. Some marine CAD systems allow users to define their own cutout standards through an External Cutout Definition Facility, making it easier to adapt to different shipyard practices.
3. Fully Custom Cutouts π
For unique structural arrangements, designers can create completely custom cutouts using geometric macros. These macros allow for arbitrary cutout shapes that are not part of standard libraries, ensuring flexibility in complex ship designs.
Regardless of the method used, all cutout types can be applied to both plates and profiles.
Clips (Collars) in Marine CAD Systems π§
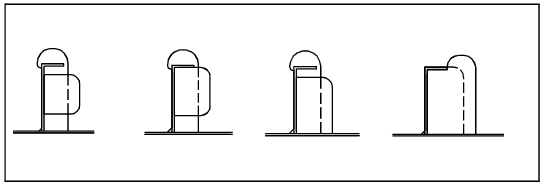
Definition and Purpose
A clip (also known as a collar or lug) is a small plate piece used to reinforce and seal a cutout. Clips serve several important functions:
- π Strengthening the area around a cutout
- π‘ Sealing gaps to maintain structural integrity and watertightness
- π© Providing additional welding surfaces to improve joint quality
- π Reducing stress concentration by distributing load more evenly around the cutout
Clips are typically welded around the cutout to provide extra support. Depending on the design, they may overlap the penetrated plate or be inserted within the cutout without overlap.
Types of Clips
Marine CAD systems support various clip types, which depend on the geometry of the cutout and the type of structural profile involved. Common types include:
- Overlapping Clips β Extend beyond the cutout edges for additional strength and welding area.
- Inserted Clips β Fit inside the cutout for a flush finish, often used where external obstructions must be minimized.
- Full Collars β Enclose the entire cutout for maximum reinforcement, commonly used in high-stress areas.
Standardization of Clips
Clips are designed based on shipyard standards and follow specific rules regarding:
- π Material properties (thickness, steel grade, and welding characteristics)
- π Geometry dependencies (clip shape varies based on cutout and profile type)
- π₯ Welding specifications (bevel types, weld gaps, and fillet requirements)
- π Corrosion protection (coatings and treatments applied to prevent deterioration in marine environments)
Most marine CAD systems allow designers to select from predefined clips while also offering customization options for shipyard-specific requirements.
Conclusion β
Cutouts and clips are fundamental elements in ship structural design, directly affecting manufacturing efficiency and structural performance. Marine CAD systems provide powerful tools for defining and managing these components, ensuring consistency and reducing production time. Properly designed cutouts and clips not only enhance structural integrity but also streamline the shipbuilding process by improving assembly accuracy and reducing rework.
By understanding and applying cutouts and clips correctly, ship designers can enhance design precision and shipbuilding efficiency.